Moving concrete giants with ease: Handling equipment from DEVO-Tech
Anyone who has ever been to a segment factory can certainly confirm that the dimensions are sometimes very impressive. With a tunnel diameter of just under 10 metres, for example, depending on the segment design, a single concrete segment can weigh up to 15 tonnes, as much as a small passenger plane. If you imagine the distance the segments have to travel from concreting in the formwork to installation in the tunnel, it quickly becomes clear that reliable equipment with sophisticated technology is required to master this logistical challenge. Welcome to the world of segment handling equipment from DEVO-Tech!
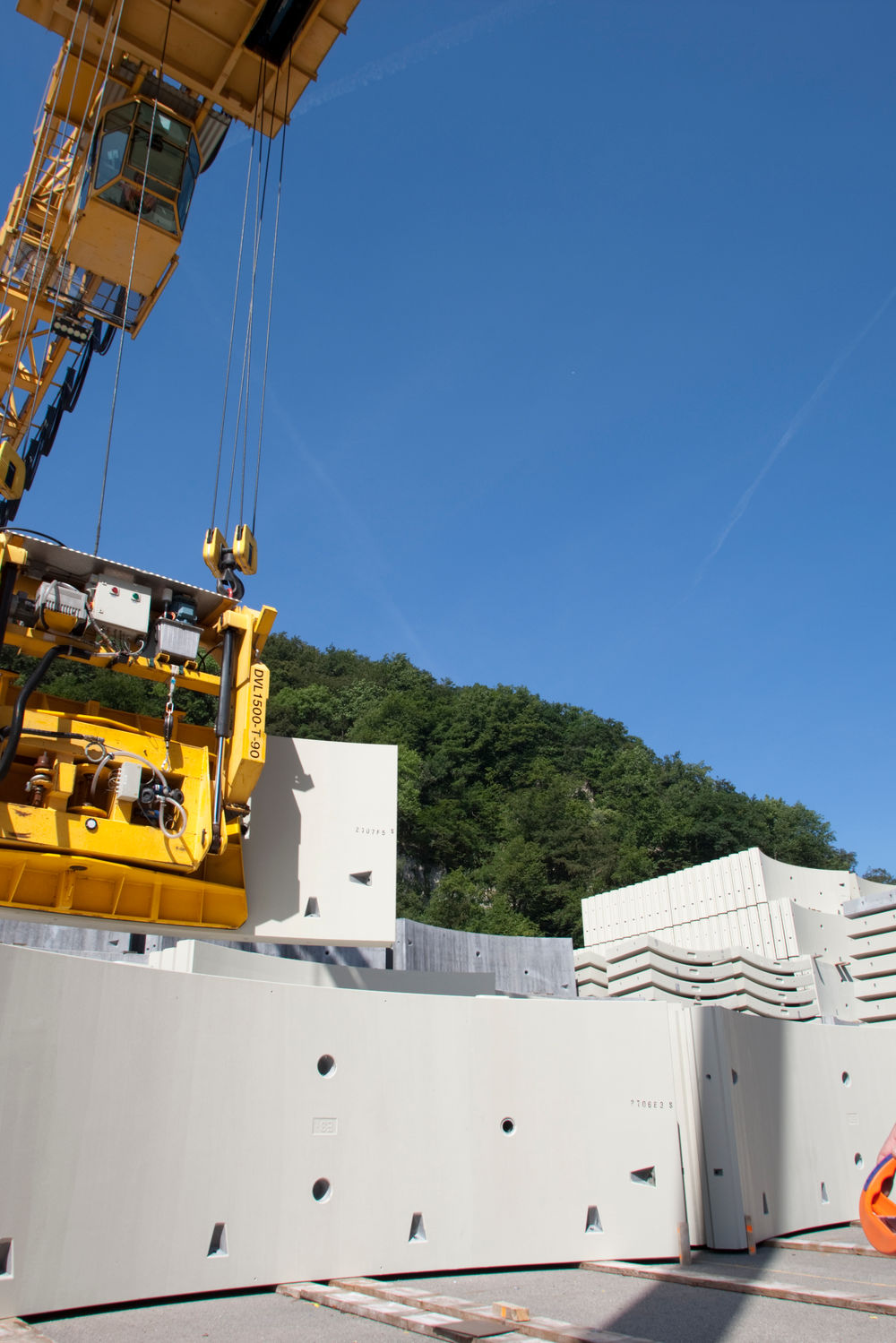
Careful, fragile!
Challenges in segment handling
Gentle handling of fresh segments
At first glance, the massive concrete giants may appear indestructible: Precise edges and smooth surfaces indicate the high quality of the segments. However, caution is required during and after stripping the fresh segments. Even if the concrete is cured as far as possible in the formwork in a curing tunnel or by means of stationary heating under the mould, it is still sensitive. Uneven load distribution, for example, can lead to stresses and spalling. We prevent this risk with the three-part vacuum suction plates on our lifting devices. The automatic segment recognition of the suction plate maximises safety during handling and transport.
Sophisticated logistics for an end-to-end process
No two segment factories are the same. When installing the equipment in an existing concrete plant, for example, separate bays, the height of the hall or narrow passageways limit the freedom of planning. The aim here is to maximise the efficiency of the production chain with the available options. If the construction company or consortium builds a field factory directly at the tunnel portal, the planned tunnelling speed and thus the daily demand for segments usually play a decisive role in the design of the factory. In both cases, the handling equipment makes a significant contribution to smooth production. We see it as our task to contribute to the success of tunnel projects with our proven standard models or customised new developments.
Continuous further development and optimisation
Standing still is a step backwards. That is why we are constantly optimising our devices on the basis of our customers' experience and further developing tried-and-tested solutions with new technologies. Safety is our top priority at all times. As we attach great importance to the sustainable and cost-efficient use of our appliances, we offer standard solutions where possible. As solution-orientated mechanical engineering experts with extensive experience, we also work on new customer-specific developments - always with an eye on costs and efficiency. Our high level of vertical integration, short decision-making processes and, last but not least, our large stock of important purchased parts and semi-finished products are of great benefit to us and, above all, to our customers.